Springs that are cycled between two loads need to be checked at the spring design stage for the possibility of fatigue.
Rockford Spring Company does this routinely as part of the spring design process. Our spring design program produces a Goodman diagram automatically for each spring design checked. This assures that this step cannot be overlooked.
Goodman diagrams are derived from S-N data after extensive cycle testing done in the spring industry over many years. The best-known reference for Goodman diagrams is probably the SAE Spring Design Manual AE-21.
An example of a typical Goodman diagram produced by our software is shown below. This diagram shows a music wire spring loaded from 22% of its minimum tensile strength at load point 1, to 44% of its minimum tensile strength at load point 2. As you can see, the resulting plot ends up on the 1,000,000-cycle line.
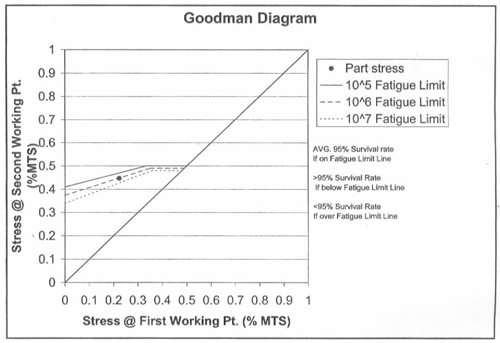
Interpreting the Goodman diagram:
To interpret a Goodman diagram we need to understand several things.
First, these charts are for a B-10 fatigue life, meaning that we would expect 10% failures at this service level. Naturally, we would like to see the plot significantly below the 1,000,000 line if we need 1,000,000 cycles.
Second, notice how close together the lines are for 100,000 cycles, 1,000,000 cycles and 10,000,000 cycles. This means that any small change in stress (or any other of a number of factors) can greatly change the cycle life. This is why the cycle life of test springs can vary dramatically from one batch of springs to the next. Two orders of magnitude or more is not uncommon. One order of magnitude or more is not uncommon even within samples from the same batch.
We must also keep in mind that the Goodman diagram represents ideal test conditions. Ideal test conditions would include no corrosion, no shock loading, no nicks or scrapes in the wire, etc. The springs would be cycled with harmonic motion at a speed less than one thirteenth of the natural frequency of the spring. There would be no buckling or non-axial forces.
Unfortunately, these ideal conditions don't always exist in the real world. The moral of the story is to be conservative with the stresses. Don't design just within the Goodman diagram without being aware of all of these other factors.
Cycle testing:
When cycle testing springs, it is always best to cycle test in the application. When this is not possible, care must be taken to duplicate the application as closely as possible. This includes the type of motion and the speed, as well as, fixturing and lubrication, etc.
One common misconception is that we can test 20 springs to 10,000,000 cycles and determine that we have verified the design, and we can be assured that we won't have any fatigue problems in the future. Nothing could be further from the truth. If we want to have any safety factor at all we need to test at a significantly higher stress and/or number of cycles than expected in the application.
Rockford Spring Company can work with you in determining appropriate test criterion. It is not unusual to have a complaint of a broken spring either in the field or in a cycle test and be told, "We have never had any failures before". The truth is, they may have just been lucky before. If you only know that the springs haven't failed, but you don't know how much safety factor you have, you are just counting on luck.
An even more elaborate test process is to do a Weibull analysis. A Weibull analysis is considerably more expensive than a simple cycle test because it involves testing to failure at several different stress levels. This type of analysis can be done to actually predict the probability of failures at different stress levels and numbers of cycles. This can be used to test an existing design or to design to an acceptable probability of failure on a new design. Obviously, a single test of 20 pieces at the same stress as the application does not guarantee a very low probability of failure.
Improving fatigue life:
There are several methods that can be used for improving fatigue life.
- Lower stress: The most obvious way to improve fatigue life is to design a spring with a lower stress. Rockford Spring can help in this regard. If room permits, we can design with a larger wire diameter or lower final load. Unfortunately, sometimes the only way to reduce the stresses is to allow more room for the spring. This is much easier to do in the early design stage. Contact us early in the process to make sure we are allowing enough space to design a spring that will have a robust design.
- Shotpeen: Shotpeening can greatly improve the fatigue life of springs. See our Shotpeening page for more information.
- Pressing: Springs can be 100% pressed solid either as a part of the installation process or as a secondary operation during manufacture. The set taken during pressing must be allowed for in the coiling process so that the correct loads are obtained after press.
- Material: We can often upgrade material to a higher tensile range or a higher quality grade. Valve quality material is used in very critical applications. The surface of the wire is shaved before the final draw to eliminate surface defects (effective but expensive).
- Dynamic loading: Shock loading and resonance can seriously reduce cycle life. It is important to avoid both situations for good fatigue life. See our Dynamic loading page.
- Application improvements: Sometimes a fatigue problem is due to something in the application that can be improved. Stress corrosion, buckling, coil clash, wear, non-axial forces, and dynamic loading are all possible problem areas that can often be improved.
Contact our Engineers for help with your specific application.